
Technologies
Use of the latest technologies and production procedures and independent tool and special machine construction form the basis for the high quality of our packaging systems.

Extrusion blow moulding (EBM)
In extrusion blow moulding, the material is extruded into a parison. The parison is then clamped into a mould and blown into its final shape. A typical feature of packaging made using this technology is the welding seam at the base of the bottle.
- Benefits: variety of designs (round, angular, oval, with handle), flexible production output.
- Products: bottles and packaging for cosmetics, household products, drinks, and food as well as oils and lubricants.
- Plastics used: HDPE, LDPE, PP, and extrudable PET.
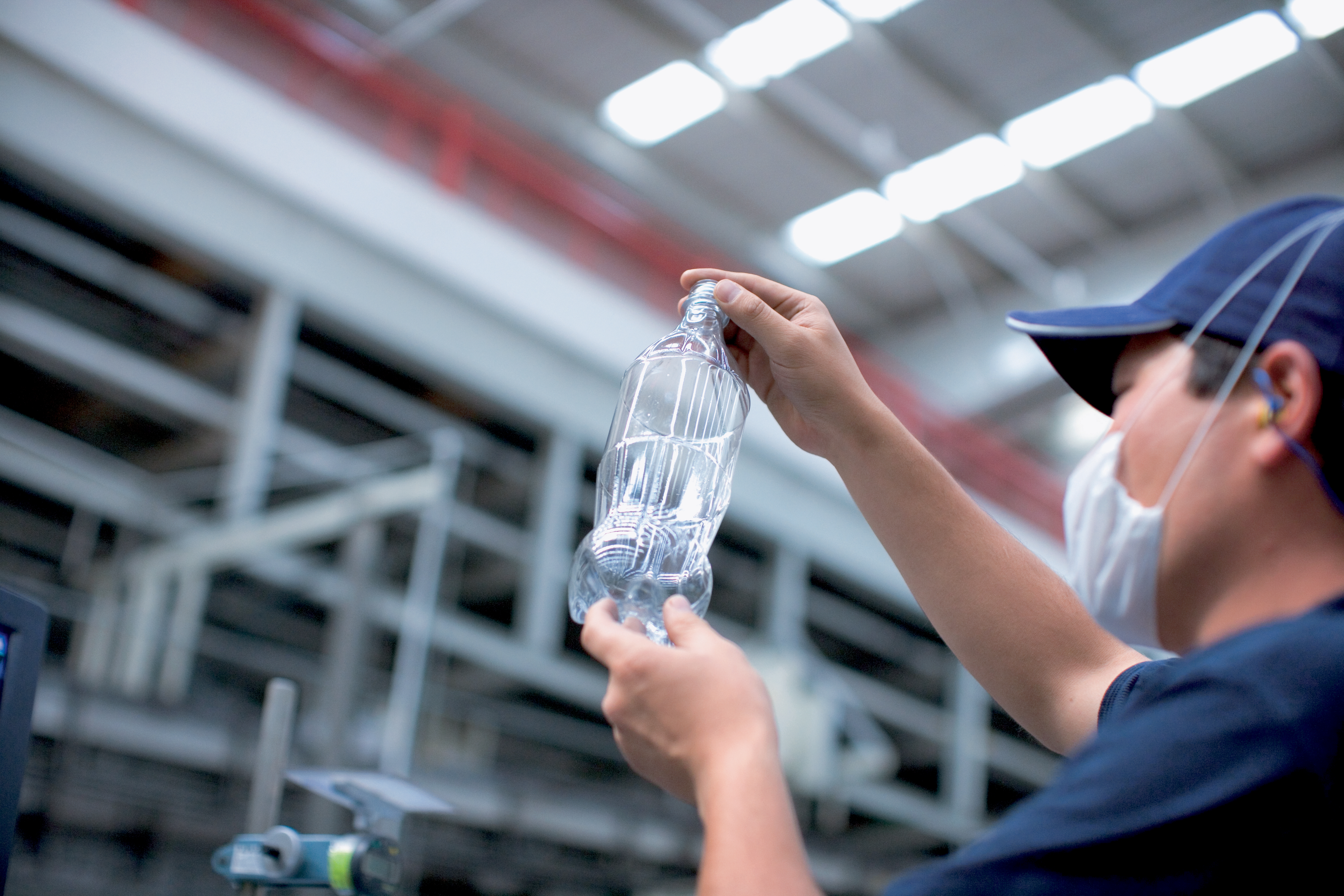
Injection Stretch Blow Moulding (ISBM) 2-step
Preforms are first produced in the injection-moulding process. In an independent, second step, known as stretch blow moulding, the preforms are reheated and stretch-blown to the final shape in the blow cavity. These bottles have a clearly distinguishable injection point at their base.
- Benefits: rapid cycle times, high output quantities, in-house and in-line solutions possible.
- Products: bottles for beverages, home care, and personal care products.
- Plastics used: PET, PS, PP, PE.

Injection Stretch Blow Moulding (ISBM) 1-step
Preforms are first produced in the injection-moulding process. Directly afterward, the tempered and still soft preform is stretched and blown to the final shape in the blow cavity. In 1-step moulding, these two steps are carried out in one machine. These bottles have a clearly distinguishable injection point at their base.
- Benefits: premium surface quality, no transfer ring necessary.
- Products: high-end cosmetics, wide-mouth jars, pharmaceutical packaging.
- Plastics used: PET, PE, PP, PS, etc.
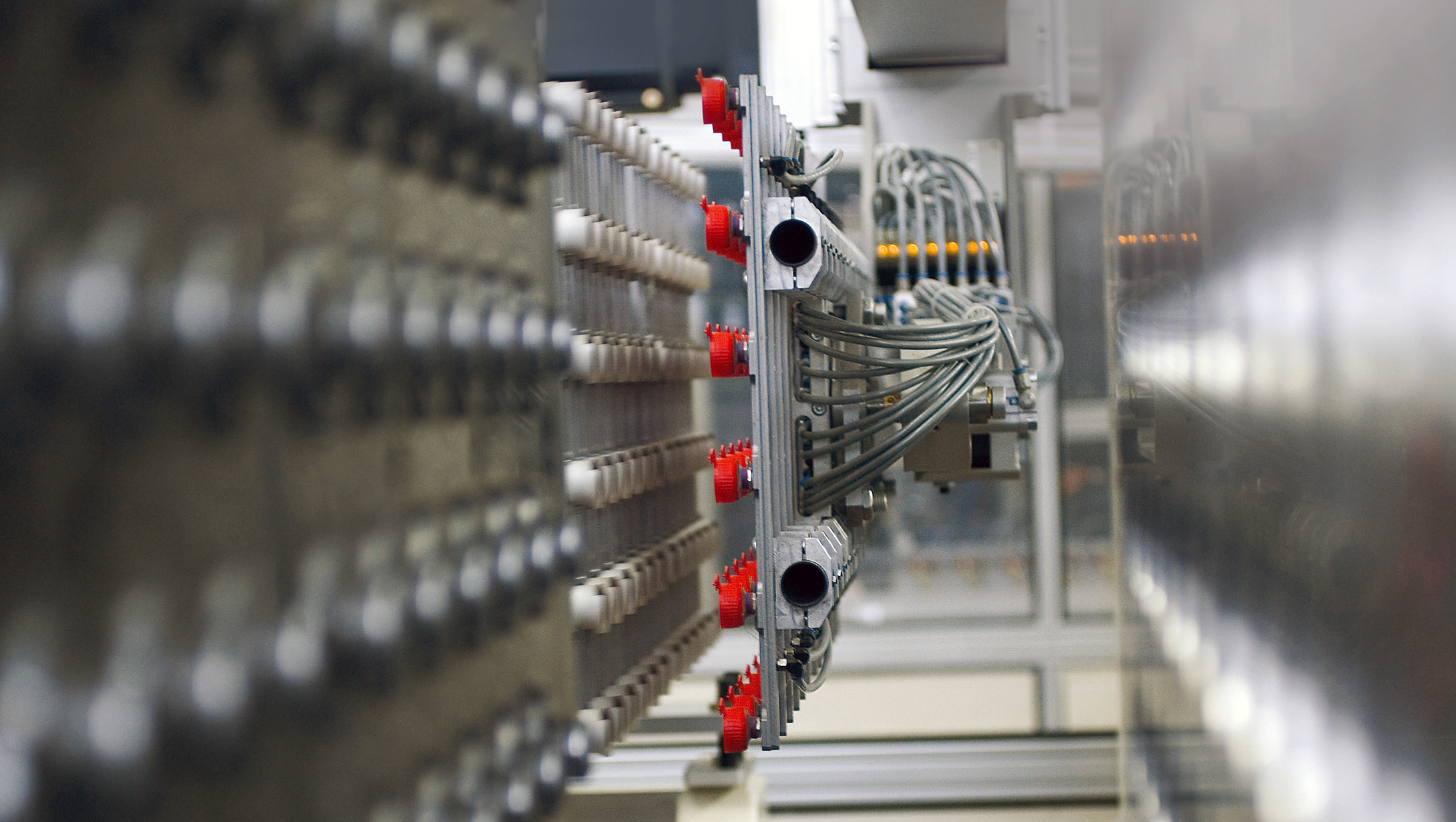
Injection Moulding (IM)
Injection moulding is the high-pressure injection of the raw material into a mould, which shapes the polymer into the desired form.
- Benefits: a virtually open choice of shapes and surfaces.
- Products: individual, technical components and closures.
- Plastics used: PP, PE, PS, etc.
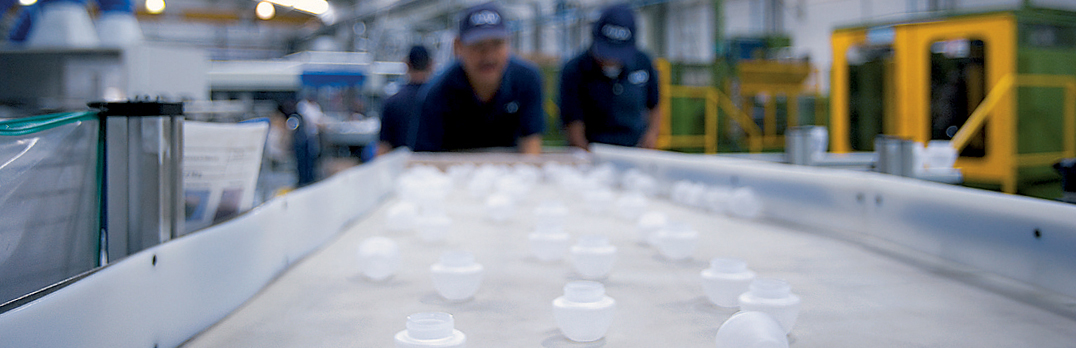
Injection Blow Moulding (IBM)
For smaller containers with high-quality standards, ALPLA uses the 1-step injection blow moulding process at selected locations. In this process, a preform is first produced, which is then immediately passed to a moulding tool and blown into the final shape.
- Benefits: high dimensional accuracy, low weight fluctuation, good finish quality.
- Products: jars for cosmetic products, roll-on deodorants, containers for pharmaceutical products.
- Plastics used: PE, PP, PET.